Annual reports
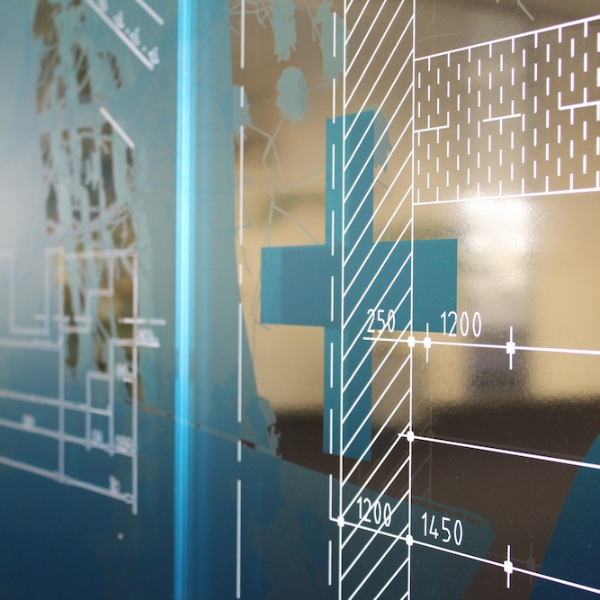
Annual environment report
To help meet its ambitions in the area of corporate social responsibility, Witteveen+Bos Raadgevende Ingenieurs B.V. mapped out the CO2 emissions from its activities in the Netherlands for the first time in 2008. Since 2016, the annual environmental reports have included the emissions inventory (CO2 footprint), the objectives and the progress on these objectives:
- Annual environment report 2022 (only available in Dutch)
- Annual environment report 2021 (summary)
- Annual environment report 2020 (only available in Dutch)
- Annual environment report 2019 (only available in Dutch)
- CO2 footprint report July 1st 2019 - June 30th 2020 (only available in Dutch)