3D Concrete Printing
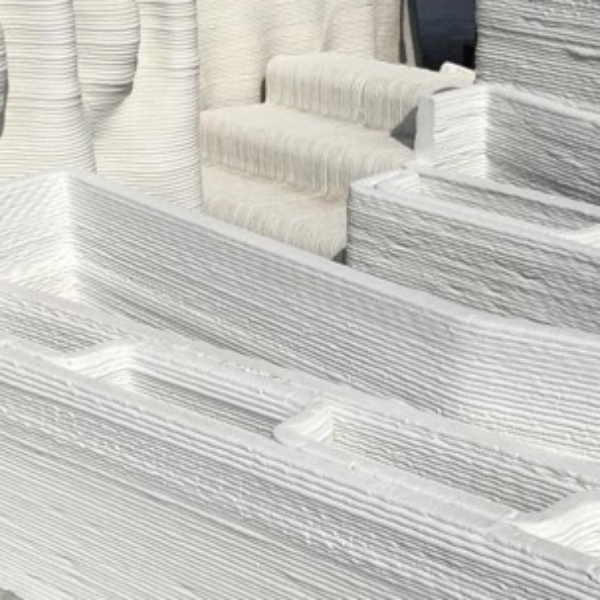
The global shortage of housing, the limited natural resources for construction, the energy crisis and the shortage of labour are all problems that require a solution. 3D Concrete Printing has the potential to address each of these problems and bring added benefits such as the added complexity and variation of designs.
Sustainable 3D Concrete Printing, lesser material and little manpower
A big advantage of 3D Concrete Printing is that fewer building materials are needed for production, because material can be printed only in the places that it is necessary for structural or architectural purposes. To continue, this process also requires no formwork. This results in less waste and less use of scarce raw materials, which improves the sustainability of the resulting object. Because the design is loaded directly into the robot and the robot then works autonomously, little manpower is needed for production. The technology makes it possible to work almost completely digitally. This is a major advantage, because the construction sector is facing a shortage of manpower.

How 3D Concrete Printing is applied
Due to the flexibility of design, 3D Concrete Printing can be used in many different projects such as urban furniture, buildings, bridges, stairs, or breakwaters. The shape, the thickness of the layers, the height of the layers, the amount of material per design can be adjusted based on the project and its requirements. Furthermore, because it is an additive manufacturing process, 3D Concrete Printing also allows to create unique objects that would otherwise be hard and expensive to produce using traditional methods.
3D concrete printing is also suitable for building houses. To speed up and facilitate the design process, an online tool has been developed: '3DCP house design tool'. Various parameters can be entered manually, such as the location of the windows and the pressure of the wind on the building. The tool then displays the stress distribution and maximum stress values of the printed walls, which helps to to make design choices within a few clicks.

How does 3D Concrete Printing work?
All parties - constructors, engineers and designers - are involved in the design process, resulting in better and optimal designs that can address the various challenges of the construction industry. 3D concrete printing supports a highly integrated and iterative design process. The direct transition from a 3D design on the computer to execution by the robot means that the design and production processes are closely intertwined. When the design is final, it is uploaded into the robot. After that, a concrete mix is placed into a pump system, that is connected to the robot via a hose. When printing is started, the robot follows the contours of the design to build up the entire design layer by layer.
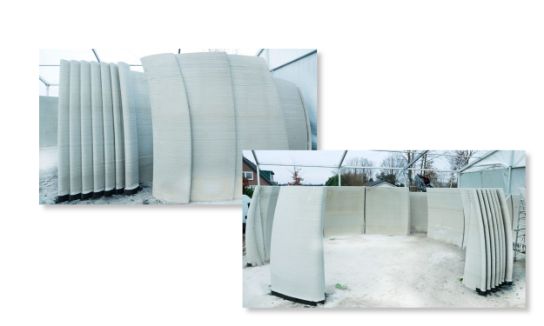
Our Slicer software
Every 3D concrete printing system comes with its own set of integration tooling and capabilities, a customised slicer software is therefore needed to configure the best suitable digital workflow for each 3D concrete printing system. Our Slicer software is a Rhino/Grasshopper plugin that essentially allows users to control 3D concrete printer and convert common 3D models to robot-readable files. From design to production, the Slicer software ensures a seamless and customisable workflow. With its user-friendly interface, the Slicer software facilitates the planning and execution of robotic production processes in a parametric design environment.

Buckling Simulation
A significant risk of 3D concrete printed structures is 'Buckling'. Because no formwork or mould is used in 3D concrete printing and the structure is produced in fresh layers of concrete by an extrusion process, there is an increased risk that the structure will collapse, deflect or buckle. The Buckling Simulation software offers a solution by digitally predicting in advance whether the concrete structure will sag and/or buckle. This minimises the risk of unnecessary material loss and provides quick insight into improving the 3D concrete printing process. The Buckling Simulation software simulates the concrete mechanism within seconds. In addition, designers can perform extensive analysis within the software design environment, so the Buckling Simulation software does not need to be linked to other software packages.

Cooperation in research
Witteveen+Bos is a partner in the 3D Concrete Printing research program with Eindhoven University of Technology (TU/e). The two main goals of this research program are to: develop 3D Concrete Printing as a viable new method to produce concrete elements and buildings, and to fundamentally understand this process.
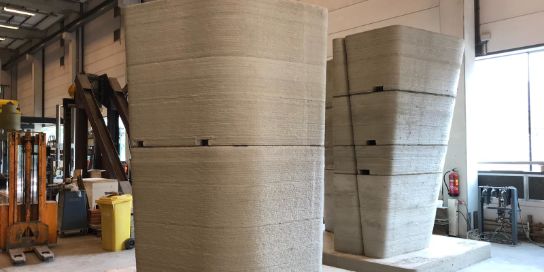
Why 3D Concrete Printing?

Solution to labour shortage
This technology makes it possible to work almost entirely digitally. As a result, little manpower is needed for production.

Less use of materials
Fewer building materials are needed, as materials can be printed only in the necessary places and no framework is required.

Versatility
3D Concrete Printing can be used to create shapes that would be challenging for conventional construction methods.
Want to know more?
Marijn generates impact through innovation such as digitalisation and 3D concrete printing in the construction industry. He was the winner of the 2020 Cobouw Young Talent Award.
