Housing construction in Singapore with 3D concrete printing
Housing and Development Board Singapore

Housing is in high demand in Singapore. Housing and Development Board (HDB), Singapore's public housing authority, is responsible for developing 80% of the houses. HDB initiated a research project to investigate the potential application of 3D concrete printing, with the aim of creating a production method that improves construction productivity and reduces dependence on foreign labour. Witteveen+Bos collaborated on this with Nanyang Technological Universities(NTU) and Robin Village.
Conventional construction methods
Currently, the design and fabrication of concrete building elements using the conventional methods of precast and on-situ production is time-consuming and requires skilled labour. Besides, the used moulds in construction will be discarded, resulting in huge material wastage.

3D concrete printing
Construction using 3D-printing, on the other hand, combines digital Building Information Modelling (BIM) technology allows automation and free-form construction without the need for moulds or formworks, thereby reducing material waste. The method opens up new opportunities for creating geometric forms that would be near impossible to create with traditional methods.
Largest 3D concrete printer in Southeast Asia
The 3D printer has been installed at the HDB Centre of Building Research (CBR). It is the largest 3D concrete printer in Southeast Asia. It can print parts up to 9 metres long, 3.5 metres wide and 3 metres high. Witteveen+Bos advised on the printer's specifications. Among other things, two room-size 3D concrete printed components were realised with this printer, the first in the world of 3D concrete printing.

Major time savings through new construction process
The entire construction process of the 3D concrete printed room, including manually inserting steel reinforcement bars into the structure and installing windows and a door, took about six days. By comparison, it would take more than two months to build a similar room using the conventional method of prefabrication. Manufacturing the prefabricated form alone takes two months.
3D Concrete Printing
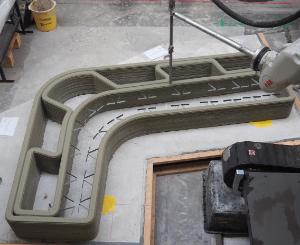
Want to know more?
Marijn generates impact through innovation such as digitalisation and 3D concrete printing in the construction industry. He was the winner of the 2020 Cobouw Young Talent Award.
